From the initial project planning to the ultimate transfer of ownership of built properties, components are always mobilized for jobs. Managing these materials and equipment is essential to the success of construction projects. This is why project asset management is a critical function
Project asset management is the process of controlling and watching over all resources used in a construction business. This covers monitoring vehicles, large machinery, tools, machinery, and building infrastructure. Given the rapid changes in technology and tightening building codes, it is critical to have the appropriate asset management systems and policies in place.
Asset management enables companies to manage their resources effectively. It aids in the expansion of business by helping the entity manage a variety of assets, including time, small assets, inventories on construction vehicles, and other parts required to complete a project.
Equipment Downtime and Its Consequences
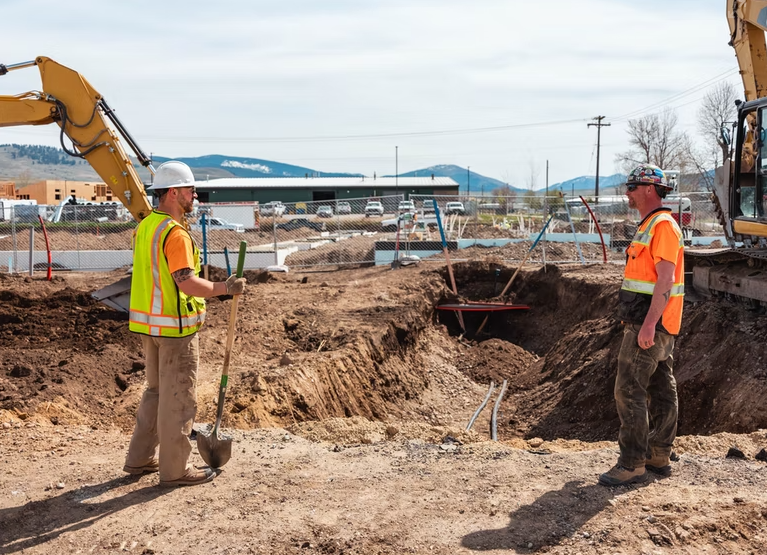
Unplanned asset downtime costs the business thousands of dollars and pushes the project farther behind schedule. Productivity will also be affected by the domino effect this will likely cause. Serious delays may start to have an impact on the workers, contractors, and other businesses who depend on the business to finish the project on schedule.
For instance, the crew might find that a big piece of equipment has unexpectedly broken when they arrive at the operations yard. Depending on the extent of the damage, this may disrupt their plans for the entire day or week. Aside from the activity hold-up, the business incurs an additional expense as it is still obligated to cover workers’ salaries even in these situations.
Safety is also an issue when machinery malfunctions on a construction site. Regular maintenance of all vehicles and equipment is the best chance to reduce downtime brought on by equipment failure or breakage. This also maintains a fair degree of safety for the employees using them. It is essential to plan and conduct regular equipment inspections and schedule all necessary repairs. The company will better manage expenditures and schedules by setting aside time for downtime.
How to Prevent Costly Equipment Downtimes
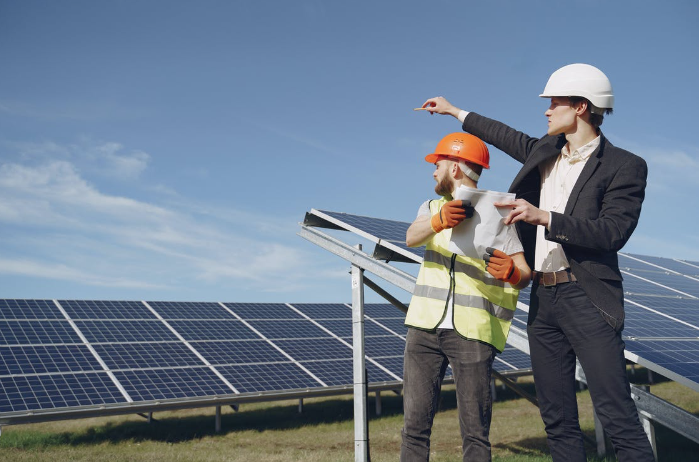
There are various ways a construction company can prevent costly equipment downtimes. One way is by having a preventive maintenance plan. The business may boost the longevity and efficiency of the equipment while also lowering the risk to people and assets by putting time and effort into a robust preventive maintenance program. It aims to prevent problems rather than deal with them when they arise. This program can assist the business in staying on top of things.
Secondly, the business can spot problems before they get worse by keeping an eye on the machine’s performance. Operators are frequently the first to notice if anything is off. Discuss the performance of each piece of equipment with the operators if the business is not the one in charge. When they point out a problem, the business should fix it as soon as possible.
Another way is to schedule regular inspections for critical equipment. Setting up a routine assessment schedule and then carrying out the tune-ups keeps the equipment in good working order.
The likelihood that a piece of equipment may fail increases significantly when it has been operating well past its projected useful life. Therefore, an asset lifespan and cost analysis are also helpful in tracking the remaining times the asset will still be safe to operate.
An asset that is not properly maintained might wind up costing the company thousands more than it would if it were maintained and repaired regularly. These techniques can help project managers comprehend how an asset’s age, usage, and condition can impact how much it can bring to the company.
Construction Management Software
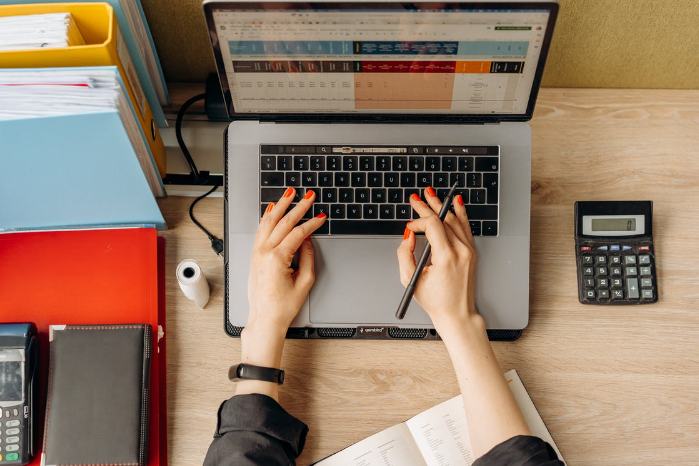
Besides the abovementioned, investing in construction management software also helps the company avoid unnecessary asset failures. This tool makes it easy for the business to create a maintenance schedule that automatically alerts key personnel when each asset needs maintenance. With it, malfunctions at inconvenient times or places are avoided.
Instead of dealing with a humiliating and expensive failure in the middle of a project, the business may maintain or service assets before they break. The software enables team accountability and ensures that inspections are completed on time. For instance, managers can set maintenance alerts to make sure that the staff never forget when and what to do an inspection.
Moreover, software with an asset management function also allows the monitoring of the age and type of maintenance a machine has received over its lifetime. Some software choices can even predict an asset’s estimated lifespan and its probability of failure, giving the business a quick overview of which equipment the business needs to replace first.
Software systems like Bizprac even provide a capability to manage equipment warranties. This enables the company to benefit from the vendor’s complimentary service and maintenance. It can also oversee each asset’s depreciation status, both at financial and physical levels. Additionally, it provides details regarding an equipment’s operating cost per hour, so owners can avoid losing money when quoting usage hours for a job. These advantages allow the construction entity to effectively manage its resources, prevent unnecessary costs, and maximize profits.
Conclusion
Equipment damage is sometimes unpredictable. But with some preparation, forethought, and management, the business can keep all of its assets in good, secure, functioning, productive, and efficient condition. Investing in software that provides project asset management functions provides the business with the capacity to avoid costly equipment failures. Fortunately, solutions like Bizprac provide this feature and other construction project management functionality.
Bizprac is an Australian-owned and operated construction management system designed specifically to support the Australian construction industry. It is a fully integrated and constantly developing software system that offers comprehensive features like estimating, job costing, accounting, single-touch payroll, purchasing, builder retentions, etc. Bizprac is designed to ensure users make the maximum profit on each project. It is also backed by an industry-leading Australian-based support team that knows the industry inside and out.
Request a free trial today or contact us at sales@bizprac.com to get in touch with one of our team members.